A Thorough Checklist for Effective Welding Evaluation Practices
In the world of welding, the integrity of frameworks is critical, demanding an extensive approach to examination methods. Discovering these vital components can produce insights that profoundly effect welding procedures.
Comprehending Welding Specifications
Welding requirements play an essential duty in ensuring the high quality and safety of welded elements and frameworks. These standards develop the criteria for materials, treatments, screening, and evaluation, consequently providing a framework for constant quality control in welding processes. Numerous companies, including the American Welding Society (AWS), the International Company for Standardization (ISO), and the American Culture of Mechanical Engineers (ASME), have established thorough standards that regulate different facets of welding.
Recognizing welding standards is vital for specialists in the area, as adherence to these standards minimizes the danger of flaws and failings in bonded joints. These criteria cover specific needs for weld high quality, consisting of appropriate resistances, the kind of welding strategies to be used, and the qualifications needed for welders and examiners.
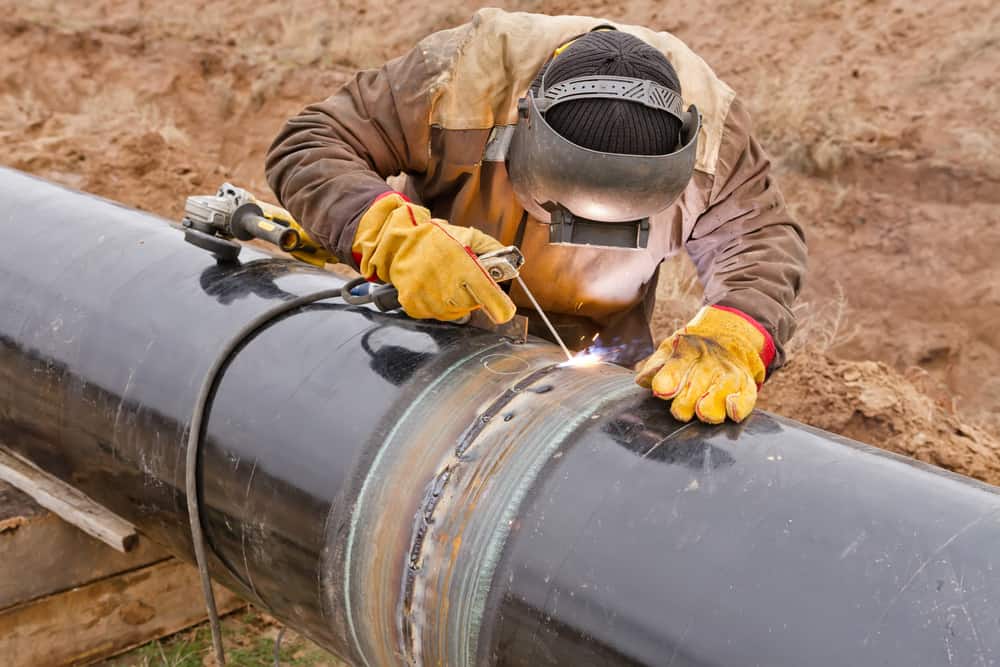
Pre-Welding Evaluation Actions
Before any type of welding procedure begins, a thorough pre-welding assessment is important to determine potential problems that might compromise the high quality of the weld. This first step functions as a critical foundation for making sure compliance with appropriate welding codes and criteria.
The initial step in the pre-welding inspection is to confirm the products being made use of. This consists of monitoring for the right kind and grade of metals as specified in the job documents. Next off, it is crucial to check the fit-up of the parts to ensure proper positioning and joint arrangement. Imbalance can lead to inadequate penetration and structural weaknesses.
In addition, evaluating the cleanliness of the surfaces is vital; contaminants such as corrosion, paint, or oil can negatively impact the quality of the weld. Following this, an extensive evaluation of the welding devices need to be conducted, guaranteeing that it is calibrated and in good functioning problem.
Finally, examining the certifications of the welding personnel is vital. Welders should possess the necessary certifications and experience to execute the details welds required for the project. By sticking to these pre-welding assessment steps, the probability of issues and failures in the final weld can be dramatically minimized.
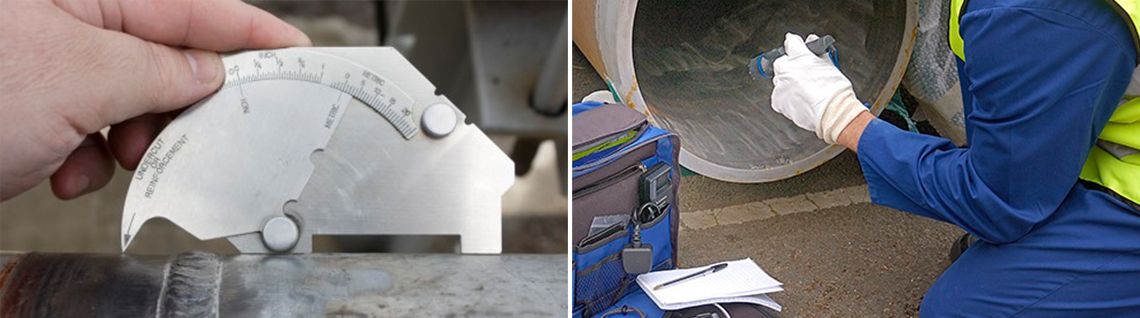
In-Process Examination Methods
In-process examination techniques play a crucial duty in guaranteeing the stability and top quality of welds as they are being performed. These methods permit inspectors to identify flaws or inconsistencies from specifications in genuine time, consequently ensuring and avoiding expensive repair services adherence to layout needs.
One key technique involves visual evaluation, where examiners examine the weld bead for uniformity, penetration, and proper profile. This can be complemented by the use of evaluates to determine weld dimensions, making sure conformity with established resistances. Furthermore, the application of non-destructive testing (NDT) techniques, such as ultrasonic testing or magnetic particle testing, during the welding procedure can disclose subsurface imperfections that might not show up on the surface.
One more essential aspect is keeping track of welding parameters, including voltage, amperage, pop over to this web-site and take a trip rate. Consistency in these specifications is crucial for achieving optimal weld top quality. Recording these specifications during the welding operation gives a deducible record for future reference.
Educating workers in appropriate evaluation strategies and the usage of proper tools boosts the performance of in-process assessments. By integrating these techniques, companies can achieve better welds, decrease rework, and inevitably make sure the security and reliability of bonded structures.
Post-Welding Top Quality Checks
Complying with the completion of welding procedures, post-welding quality checks are essential to confirm that the welds meet all defined requirements and needs. These checks are crucial for guaranteeing the integrity and toughness of the welded joints. The examination process commonly begins with an aesthetic evaluation, analyzing for surface issues such as cracks, porosity, or insufficient blend.
Ultimately, non-destructive testing (NDT) methods, such as ultrasonic testing, radiographic testing, or magnetic fragment testing, might be employed to discover internal imperfections that are not noticeable to the nude eye. Each technique has its distinct benefits and is selected based upon the weld's area, material type, and the nature of the application.
In addition, verifying dimensional accuracy is a vital aspect of post-welding high quality checks. This includes gauging the weld's dimension, alignment, and profile to ensure compliance with engineering specs. Lastly, analyzing the mechanical buildings of the weld, consisting of tensile toughness and ductility, can provide additional assurance of performance under operational conditions. Generally, detailed post-welding inspections are vital for maintaining safety and security, adherence, and efficiency to regulatory and sector criteria.
Documentation and Reporting
Exactly how can effective paperwork and reporting enhance the welding assessment process? Precise documents and extensive coverage are vital elements that ensure the stability and top quality of welding operations. Welding Inspection Milwaukee. They function as an official record of assessment searchings for, promoting liability and traceability in compliance with industry requirements

A well-structured coverage system allows inspectors to plainly connect any non-conformances, inconsistencies, or locations needing renovation. This openness cultivates an atmosphere of constant enhancement, as stakeholders can easily analyze previous efficiency and apply rehabilitative activities.
Moreover, effective documentation includes comprehensive records such as welding procedure specifications (WPS), welder qualifications, and inspection checklists. These components give a structure for examining weld top quality and adherence to developed guidelines. In case of disputes or quality concerns, detailed documents works as a trusted referral, minimizing uncertainty and safeguarding all parties entailed.
Last but not least, preserving organized documents aids in training and accrediting personnel, ensuring that sector finest practices are promoted. Eventually, precise documentation and reporting investigate this site not just improve the welding inspection procedure however additionally add to the overall safety and security and dependability of welded frameworks.
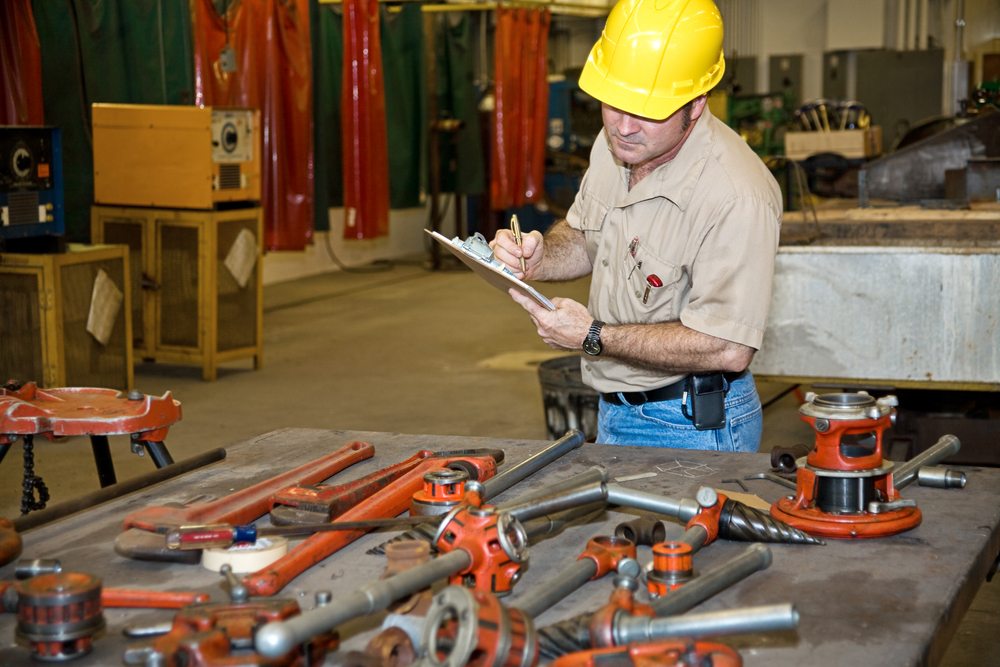
Final Thought
In verdict, an extensive checklist for effective welding inspection practices is essential for making certain top quality and security in welded structures. Adherence to developed welding criteria, careful pre-welding evaluations, rigorous in-process evaluations, and thorough post-welding top quality checks jointly contribute to the honesty of bonded joints.
Welding criteria play a crucial duty in guaranteeing the high quality and safety and security of welded components and frameworks. over at this website Numerous organizations, consisting of the American Welding Culture (AWS), the International Organization for Standardization (ISO), and the American Culture of Mechanical Engineers (ASME), have created thorough requirements that control various elements of welding.
Adhering to the conclusion of welding operations, post-welding quality checks are crucial to validate that the welds fulfill all specified demands and standards - Welding Inspection Milwaukee.In final thought, an extensive list for reliable welding assessment practices is essential for making sure top quality and safety and security in bonded structures. Adherence to established welding standards, meticulous pre-welding inspections, rigorous in-process examinations, and extensive post-welding high quality checks collectively contribute to the honesty of welded joints